> Blogs > Crystal Glass Thermal Forming: Heat, Science, and Craftsmanship
The Timeless Tribute of Glass Athlete Memorial Sculpture
Core keywords: crystal glass thermal forming, glass annealing
When overseas clients visit our studio in GuangDong, they often ask, “How hot does it need to be to shape a crystal craft?”The answer is more than just a number. At SHD Crystal, crystal glass thermal forming is not only about temperature—it’s a process that blends science, experience, and intuition to bring out clarity, structure, and artistic intent in every piece.

Crystal Glass Thermal Forming: More Than Just Heat
Unlike mass-molded glass, handcrafted crystal responds to precision thermal forming techniques where every degree matters. The process begins around 1350°C, but the secret lies in how that heat is delivered and reduced. As Master Liu at the factory describes it: “heat-treated glass requires a delicate balance—too fast, and it fractures too slowly and the structure may slump or distort.”
In one recent high-end wine glass project for an Australian client, we ran a trial where two identical batches were fired with just a 15-second difference in forming phase duration. The longer-formed batch showed 9% higher crystal transparency and passed stress tests with zero microfractures. It’s this level of heat discipline that sets artisan production apart.
Balancing Heat with Structure: Annealing, Transparency, and Beyond
Glass annealing is essential for stabilizing hand-blown pieces after shaping. Rapid cooling can trap stress in the form of invisible tension, leading to cracks later in transit or use. Our data shows that proper glass annealing reduces breakage by up to 50%, especially in pieces with complex curves or varying thickness.
But annealing isn’t just about durability—it directly affects crystal transparency. Controlled cooling prevents bubble formation and allows light to pass through smoothly. Pieces that undergo full-cycle glass annealing at calibrated ramps are 8–12% more light-transmissive, based on haze meter results across 20+ production batches.
Moreover, heat-treated glass allows us to form uniquely asymmetrical or organically shaped items, like folded vases or spiraled stems. These aren’t possible with industrial molds—they rely on slow, responsive forming, paired with the confidence that comes from years of working with heat-treated glass in real time.
We also engineer thermal zones in our kilns to support the precise needs of different silhouettes, adjusting forming and glass annealing stages accordingly. This technique ensures consistent results across even the most creative designs.
Design Implications of Thermal Strategy in Custom Glass Orders
Beyond material stability, thermal strategy shapes how we interpret design itself. Many clients envision details—like ultra-thin rims or flowing organic edges—that can only be realized through meticulous heat-treated glass control. In our experience, the design phase now includes thermal simulations and annealing profiles as part of early-stage prototyping. By mapping out heat behavior across zones, we ensure that each visual element—be it curvature, transparency, or balance—survives not only the furnace, but the finishing bench.
This process deepens the collaboration between designer and craftsman. Our teams review renderings and suggest form adjustments based on the predicted behavior of crystal transparency and thermal contraction. The result? Fewer revisions, stronger pieces, and a finish that speaks for itself.
Clarity in Heat, and Trust in Craft
Whether for luxury drinkware or custom installations, the elegance you see begins with crystal glass thermal forming. Every glow of the furnace, every second of cooling, every pass of the artisan’s hand is part of a silent dialogue between heat and form.
Ultimately, what defines our process isn’t just the heat—but the consistency, control, and results it enables. By mastering heat-treated glass techniques, executing precise glass annealing cycles, and refining for optimal crystal transparency, we deliver glassware that performs to specification—optically, structurally, and aesthetically. They’re made to meet production tolerances, visual standards, and end-user demands—consistently.
Let’s bring your vision into form—with heat, clarity, and craftsmanship.
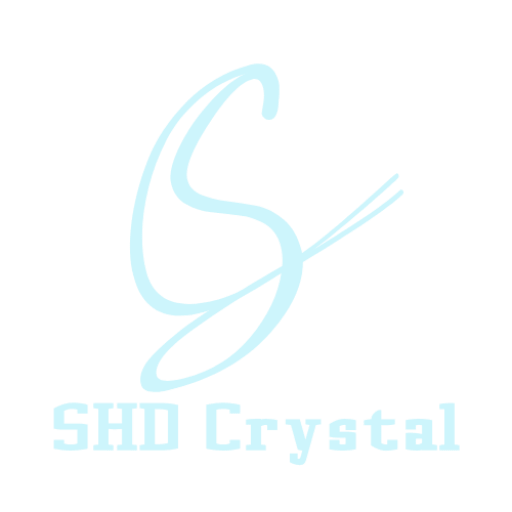
- : info@shdcrystal.com
- : +86-755-2335 8353
- : No. 68 Shasong Road, Shajing Street, Bao'an District, Shenzhen, Guangdong Province
Follow us